Using Grinder Bit To Make Holes
Drilling holes in glass can be a bit frightening to start with. Once you get the hang of it, you’ll be able to hang sun catchers and fused pieces up without unsightly hooks.
Holes in glass open lots of creative doors for you. You can insert foiled glass jewels (see below) and bolt glass shapes on to a thicker base glass. If you’re using a drill you can engrave text and images on the glass.
You can use either a grinder head or a drill. I’ll take you through both methods. You don’t need lots of expensive equipment.
- If you already have a grinder you can simply add an extra drilling bit for it and get going fairly cheaply.
- If you’re interested in engraving your stained glasswork or want smaller holes for hanging your panels invisibly, then either a Dremel or a flexible drill is the way to go.
The most crucial thing to remember when learning about drilling holes safely and without breakage is that you need water. It acts as a coolant and stops the glass from over-heating and cracking.
Click here to jump to some step by step help on drilling a larger hole for a jewel
Drilling Holes In Glass With A Grinder
- Wear goggles to protect your eyes.
- The cooling water is provided via a wet sponge that you keep under the glass.
- Introduce your stained glass slowly over the top of the drill bit at an angle to start with, and then slowly straighten it up so that it’s flat on top of the drilling bit.
- Don’t press too hard otherwise it will break. The diamond will do the work.
- Just before the drilling bit comes through the top, reduce the pressure a bit so that it doesn’t chip the stained glass.
Here’s also a helpful 52-second video of drilling holes in stained glass:
Video showing how to drill a hole in stained glass with a grinder
Grinder Drill Bit Suppliers
This is the cheapest option for drilling holes in stained or fused glass. You can buy drilling bits that fit on your grinder head, either 1/8″, ¼” or 3/8″ in diameter.
Most manufacturers supply drill bits for their grinders, so you should be able to find suitable drill bits.
You may have to buy an adapter too, depending on the make of your grinder. It can stay fixed on top of your day-to-day grinding drum, making it ready and easy to use whenever you want to drill a hole.
Amazon sell all these types of products. All you need to do is screw the Inland Bit Adapter on top of your grinding drum, and then screw the diamond drilling bit into that.
Drilling Hole With Grinder Head For Glass Jewel
One of my online students Denise Whittle has very kindly put together a step-by-step photo guide showing how she drills a hole specifically for a glass jewel.
Top Left to Right:
- shows the 3 bits. 3/4″ on the bottom, 1/8″ on the top and 1/4″ to the side. Grind your piece first to make it safe to handle then mark where to drill. Wet the part of the glass that touches the bit and the bit itself with a soaked sponge. Turn the grinder on.
- Place the glass directly on the bit. You have to keep wetting the area. So lots of stop and go.
- Start it off with a dent on Side 1. Then flip the glass over
- Sludge starts to form when the hole starts to open
- Hole is now the size of the grinder bit. Now you can rest it on the surface to grind a bigger hole. Still have to keep wetting the bit.
- Switched to the 1/4″ bit to make the hole bigger. (You could continue enlarging the hole with the 1/8 but I think you have more control and the sides stay rounder with the larger bit).
- 1/4″ bit made the hole big enough to fit over the 3/4″ bit.
- The hole being made bigger to fit the jewel used.
- To fix the jewel in you have to foil around both the jewel and the hole before soldering.
For the hole, cut short foil lengths and stick them next to each other all around the hole from top to bottom rather than sideways. - Burnish them all the way around then use a sharp craft knife to cut away the excess.
- Solder in as normal.
- Tada! The jewel fits perfectly 🙂
How To Make Holes In Glass With A Drill
Again, water is the key to safety and success. With a drill you have to keep the stained glass cool by putting it in water as you do the drilling to prevent cracking.
- Put on an apron and goggles.
- Put the glass in a shallow container. I use a plastic photographic tray, but ice cream tubs will do.
- Put a bit of newspaper or polystyrene at the bottom to stop you drilling a hole through the container.
- Cover the stained glass and paper with about ¼” (6.5mm) water.
- If you can’t find a tray big enough, simply dab water on with your left hand throughout the drilling/engraving process so that it doesn’t get hot and break.
Here’s a very helpful 2 minute video showing how to drill a hole in stained glass with a flexible shaft drill by my friends at Warm Glass, Bristol UK.
Drilling a hole in stained glass with a Dremel with a flexible drive
- Turn the drill on. The fastest speed is best for drilling holes.
- Holding the hand piece like a pen, introduce the drilling bit to the glass slowly, from the side to start with to make a small dip to prevent slipping and scratching.
- Once the hole is started hold the drilling bit vertically and let the diamond burr eat into the glass with a little bit of pressure.
- Gently move up and down, so that water can get into the hole.
- Don’t push hard or you’ll break it; let the diamonds do the work.
- When nearly through to the other side reduce the pressure even more so that you don’t chip around the hole.
Types Of Drills Available
Flexible Drive Drill
This type of drill is very similar your dentist’s drill, with a moveable ‘arm’ and a hand piece that holds the diamond drill bit.
These drills are the most adaptable of the drills available as it doubles up as an engraving tool.
The speed is adjustable with a foot pedal. Go slow to start the hole and speed up once you’ve made an initial ‘dent’. You also have fine control for engraving.
Pros
- They’re small, inexpensive and excellent for drilling smaller holes. This is great if you want to hang your glass work up invisibly with thin wire or fishing wire. Don’t forget to use a plastic gromit with fishing wire to prevent the glass rubbing and eventually snapping the wire.
You can also bolt a small shape of glass on to a base glass. - These drills are fantastic for engraving pictures or text on to the surface of the glass. You could use it for copying your children’s drawings or your favourite poem on your stained glasswork.
Stained Glass Drill Suppliers
The best quality and value drill with a flexible ‘arm’ option is the Dremel 4000. (affiliate) This set up – drill with a flexible shaft – really gives you the freedom to sign your name, copy drawings or make other marks on your glass really easily. I have a video showing you how to sign your name on glass here.
The flexible shaft that connects to this Dremel can be found on Amazon here. (affiliate)
It’s been rated 4.5 out of 5 stars by Amazon reviewers, who say it’s a “good quality tool” and “great value”.
Of course Dremels are very good drills for all sorts of craft work, not just stained glass. There is a wide range of different bits available for various jobs.
You need decent drilling bits for glass. The cheap ones go blunt quickly and end up being a false economy. Diamond bits are available from dental suppliers.
Packets of 6 diamond drill bits can be purchased but if you really want the best, you need the impregnated diamond coated bits – sintered – which cost more. I get mine from a specialist drill supplier and they last for ages.
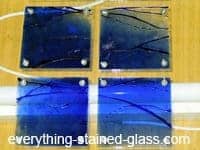
So that’s it, simple! Hopefully you’ll have a really good idea now about drilling stained glass, and the equipment you need to get started.
If you don’t already own a grinder, there’s a page of grinder reviews of the best available here.
Tech Talk – Drilling Glass
You can buy diamond drill bits with three different types of diamond coating, ranging from single layer (cheaper and not so durable) to impregnated (longer lasting but more expensive).
The diamond drill bits come in sizes from 1/16″- 2″ (3-50mm) – the bigger the bit the slower the recommended rpm.
To give you a rough guide; drill bits up to ½” (13mm) can be used at speeds from 3500-4000rpm, for ½”-1″ (13-25mm) bits go at 2000rpm, slow down to 1000rpm for drill bits between 1″-2″ (25-50mm)
1- do not use blade type of drill these type are for tile work
2-you can find 2 -3- 5 mm drill for chain scaw purpose cheap price
3- put a tape like duck tape at the site of drilling and turne tha side of tape like a pool of water
4-if the hole is big use bell type or deum type drill
5 if possible do not work only whit hand hold use a column shop drill
6- put a hard foam unther the glass do not work on hard stoff
Thanks for your additional tips Jacques. Good idea about using the tape to form a barrier and make a little pool to keep the bit cool.
Once the holes have been drilled into your glass piece is it possible to add a metal reinforcement ring to the hole ? This would give a very nice finish. Do you use ordinary reinforcement rings as used on fabric ? Does it have to be glued?
It’s a good idea but the metal could put pressure on the glass. Plastic grommets are a better bet with glass Pauline.
I few drops of oil will serve as a better lubricant than water. Plumber’s putty can also serve as a dam to help from keep the oil near the hole.
Thanks for this Stephen, both very useful additions to the page 🙂
Thank you for your excellent article on drilling holes in glass Milly. It is spot on!! I have a couple more tips, learned the hard way usually. I drill a LOT of holes in glass for my stained glass wind-chimes and sun-catchers. I feel that is a more secure way to hang than a ring caught in copper foil to me and I use #18 copper wire and glass beads to hang, not monofilament or thread so I do not worry about the glass edge cutting it. So one tip is to plan for and do the drilling after cutting a piece but BEFORE you even copper foil. That way the piece is small enough to fit in my pan of water with a thin block of wood in the bottom that I drill my glass piece with a bit of water on top. I do not have to hold my breath drilling on a lovely finished piece and hoping I will not crack it or “skitter” – a real word – when you do not control the angled bit at the beginning on the surface firmly and it travels across the glass etching a line in it, yikes. By the way, if that does happen, you can disguise it quite a bit using a toothpick in clear nail polish and carefully putting it only in the etched line. For large pieces you find you need to drill after you have finished, use poster putty to make a small dam to form a lake of water around the marked hole you are going to drill. Or use an eyedropper and continue to wet the drill bit and hole as you drill. At the last, move the drill bit around at its top and make the hole a bit bigger than the wire you are going to use so it swings freely. Also at the first sign the bit is getting dull – a skitter, taking too long to drill – please throw it away and save yourself heartbreak. The next piece will crack or skitter I promise and you will learn to do this! Depending on the glass, you may only get 5- 10 holes out of each drill bit! I just order here in the US for my Dremel, free shipping on Amazon. Solid bit 1mm -3mm kit of 30 is $24. Search for diamond drill bit.
Thank you so much for this excellent additional explanation Linda. All solid advice. I really appreciate your time, as will my readers 🙂
This video and description was so helpful. I was making the ying yang symbol for my tai chi teacher when I came across your info on the Hub. I ordered the drill bits and adapter for my grinder and was successful in drilling the holes. However I ran into a problem when I soldered the jewels in the holes. A crack occurred immediately in the inside curve of each 1/2. Note: I soldered the jewel in place before soldering the 2 halves together so wasn’t sure if that was the correct way to do it. I figured this is a learning experience and started over. I enlarged the piece to a 5″ circle and purchased a set of diamond drill bits (from Amazon for $13 that were recommended by a guy on a You Tube video) that attach to a regular power drill. I did the drilling under water and in only a couple of minutes was successful in making the holes. The circles are perfectly round with this method. Now I’m ready to solder the jewels into the holes and solder the two halves together. I’m a little nervous that I will crack the glass again. I was thinking I would go with less foil on the jewel and in the hole this time as it was a little heavy in my first attempt. Perhaps this fact increased the amount of heat and was responsible for the cracks. The jewels are faceted and measure 15 mm. Should I solder the 2 halves together before soldering the jewels in the holes to give the piece more stability?
Thanks so much for sharing your experience Charlene – even if it’s not ideal with the cracking, eek.
I wouldn’t solder the halves together as it won’t help the cracking and if it does crack again you’ll have to unsolder it.
I’d use the narrowest foil possible and turn your iron down. Don’t keep going for long, do it as quickly as you can and if you have to revisit it, make sure you let it cool in between.
I hope that helps. Let us know how you get on. Good luck!
Ok after you get the hole drilled into the glass, how is the jewel put in? Is it wrapped in foil & soldered or is it glued?
It’s a bit tricky but you have to foil around both the hole and jewel and solder.
For the hole, cut small copper bits and stick next to each other from top to bottom rather than all around. Burnish them all the way around then use an exacto knife to cut away the excess.
Very good question Linda, I’ve now added this as a bullet, thanks for asking.
Hi Milly,
My question is similar, but related to lead work. How do you incorporate a jewel into a leaded piece? Especially the smaller ones. Is it a similar technique or do you try and muscle lead came around it?
Lisa
You can bend the flange back on the lead and get the lead in like that. It’s not easy though, requires a lot of coaxing and patience.
Good question, Lisa, thanks.
This question made me wonder…does anyone ever combine foiling with lead work? Foil and solder the small pieces and use lead came on the larger pieces?
Good deducing Kathy… I have a page on foil and lead combining here:
https://everythingstainedglass.com/mixing-lead-came-and-copper-foil
Thank you, such good information!
Thanks Diana, glad to be helpful 🙂
An easy way of adding gems to glass art is to place them on a cut line. Mark the location with a Sharpie, use a ring saw to cut the semi-circle on each piece of butted glass, then even out the semi+circle for a perfect fit by using the coordinating size drill bit. I’ve been doing this for years and the “hole” is so much easier to foil.
If you look at my glass panels, you’ll see exactly what I mean.
Thanks for your suggestion Patricia. It’s the same approach as Bruce, above. I agree wholeheartedly that this is a very good and less fussy solution.
Sometimes that different colour island in a sea of glass is the only way to go though 😉 Both have their place and one isn’t better than another.
Follow up
Eternaltools.com have good selection of drills uk based
Phill.
This looks a great site, perfect for us stained glassers who want to do ‘things’ with drills! Thanks for adding this Phill, much appreciated.
Just tried Sutton tool they say that they don’t sell them
Am l looking at the wrong site?
Phill.
I see Sutton Tools have been bought out. A Google search for ‘diamond sintered burs’ throws up this one – dental tools (never thought of that!) https://www.technicare-dental.co.uk/product-category/diamond-instruments/sintered-diamond-burs/
They look about the right price – 20-25 a piece. There are 2 pages of them.
Hope that helps, haven’t tried this company though so can’t recommend personally.
What is the name of the supplier you purchase the impregnated diamond coated bits from? I drill lots of glass and would like to see what they offer. PS I love your emails they are always so informative. Thanks for the great information!
Sandy
Sutton Tools but they’re in the UK. Someone – Micky above – suggested dentist’s supply places which seemed like a brilliant suggestion. Sorry I can’t be of more help for the US.
I get my bits from TOOLORBIT located in California. They have a whole section for diamond cutting tools. I like to use 3/8 inch hole cutting bits. I also have ditched using 3/4 inch bits and mainly use 1 inch bits.
Biggest problem I have with holes is foiling the inside of hole. Mostly now just arrange a seam location so I only have to foil a semi circle.
Thanks for the supplier info Bruce, it’s always good to have suppliers all over the world for people to choose from.
I like your workaround, along a seam – very pragmatic! I love the look of the jewel being in the middle of the glass – for occasional special situations when nothing else seems to do 🙂