How To Solder Stained Glass Lead – Step By Step Tutorial
Stained glass soldering is one of the most exciting steps because it allows you to pick up your panel and see the coloured light coming through it for the very first time. Woo hoo!
Here’s where you find out how to solder stained glass so that it’s both strong and neat.
What You Need
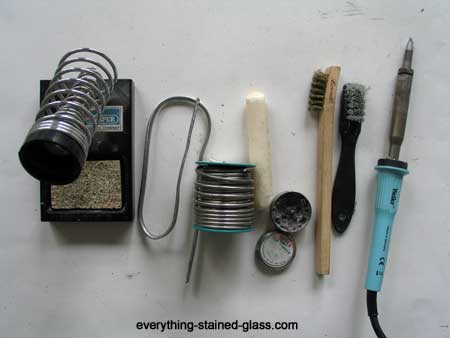
- Soldering Iron (*paid link)(at least 80W)
- Soldering Iron Stand (*paid link)
- Flux (tallow or other soldering flux such as Glastar Glasflux)
- 50/50 solder (*paid link)
- Wire brush
- Tip cleaner (*paid link)(either a commercial tinning block or a damp flannel)
- Cheap brush
Just so’s you know, if you click and buy through the link within 24 hrs I get a small % from Amazon, (not you!). Thanks in advance but no worries if you have a local store – I’d always support them first 🙂
If you’re new to using lead came as a technique I would highly recommend you give it a try. It will add a great deal to your skill set and give you the best of both stained glass worlds – foil and lead.
If you don’t have a local class my Leaded Stained Glass Artistry course has taught many people – even those who have never used lead before – how to make a stained glass panel using lead came. The course is self-paced and online so you can learn this lovely technique even if you are unable to get to a class. You can find out more about it here Leaded Stained Glass Artistry.
How To Solder Stained Glass Lead Came
1. Preparing the panel for soldering
- Turn your soldering iron on. They can take a while to heat up (although the Hakko FX-601 that I’ve started to use more and more is super quick with its ceramic core!)
- Clean each joint with a wire brush. This gets rid of any oxidation or dirt that may have built up on your lead came. You need a clean surface so that the solder will adhere properly.
- It’s best to solder immediately after cleaning. This will stop any oxides building up on your lead joints.
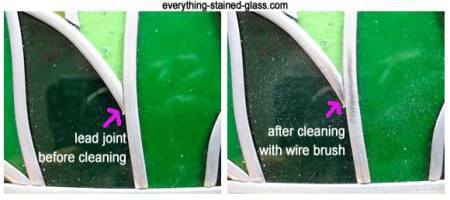
2. Using the stained glass solder
If you’re a beginner, it’s a good idea to cut off some pieces of scrap lead and practise how to solder stained glass by soldering joints along the lead. This way you can get the feel for the way the solder melts, and how hot your iron needs to be.
Soldering fumes are dangerous. Try to do the soldering process by an open window, or buy a portable fume extractor if you’re going to do large amounts.
- Brush flux on to a lead joint.
- If you’re right handed, place the end of the stick of solder right over the join with your left hand. Don’t hold it too close to the end. The solder heats up along the stick and you could get burnt.
- Bring the hot tip of the soldering iron to the solder over the join. A drop will melt off onto the joint.
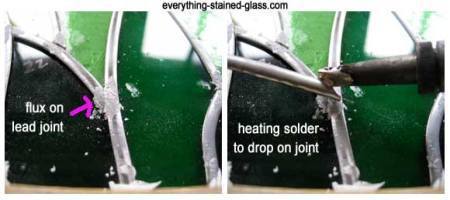
- It’s better to put a small amount on first and add more. Stained glass solder sticks to the lead and is difficult to take off if you’ve put too much on.
- Hold the soldering iron still on the solder for a few seconds, letting it find its natural level. It should be a little rounded and covering the whole of the lead join.
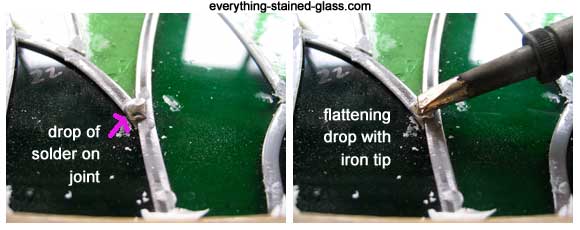
- Be careful not to take too long because the solder will melt too much and disappear through the gap.
- Both the lead and solder need to heat up for a strong union. Try not to touch the lead directly with the tip as it could melt it.
- Make sure you have soldered every joint. It’s easy to miss one or two.
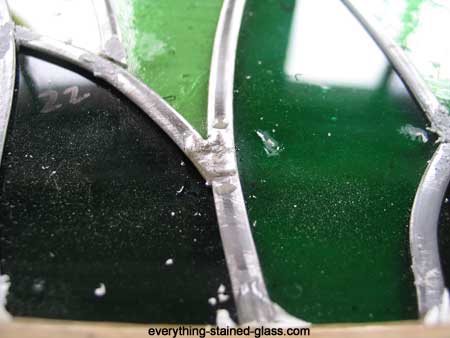
Common Mistakes Made Good
I have a video on this page here that takes you through 3 Common Stained Glass Soldering Mistakes and shows you how to rescue them.
3. Turning the panel over
- Be very careful turning your stained glass panel over. It is very fragile at this point.
- Wait until the last solder join has cooled down.
- Slide the panel slightly over the edge of your work surface and lift it upright.
- Lean it over carefully, supporting the back with your left hand.
- Now clean the joints with a wire brush and solder the back side as above.
- If you have gaps at the joins where the lead doesn’t fit very well, you can fill them in with little bits of lead cut from a spare flange. Do this one by one, otherwise they’ll fall off.
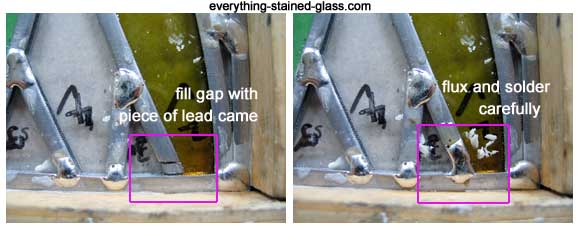
4. Cleaning the panel
- Clean all the flux off the soldered joints and lead came with the wire brush
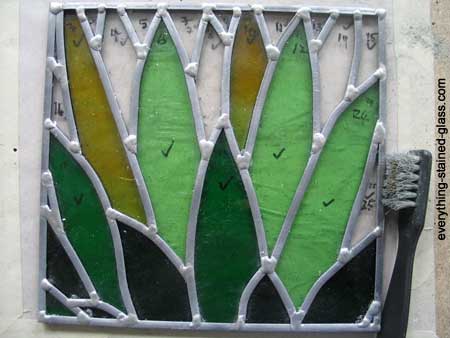
Soldering Hooks On
If your panel is for hanging in front of a window and doesn’t need to be waterproof, you can add some hooks on at this point.
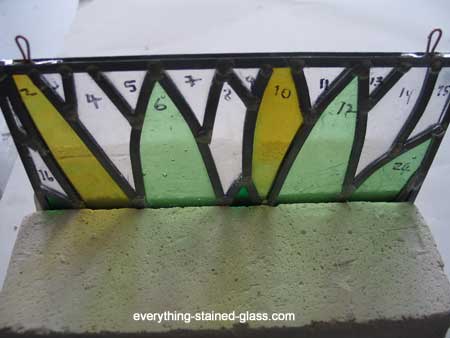
- Make or buy a couple of wire hooks
- Rest your panel upright between two bricks
- Solder the hooks carefully on to the border lead with the tip of the soldering iron held vertically.
For a detailed step by step tutorial on how to solder jump rings on to a panel go here
Troubleshooting
- Q. My stained glass soldering isn’t smooth, it’s all crinkled.
A. Either you haven’t held the iron on the solder for long enough or it’s not quite hot enough. You can re-do these joins but make sure it cools down before you redo otherwise you might melt the lead came. - Q. My joints are all messy.
A. You might be moving the soldering iron when you’re melting the solder. Add a little more solder and try to keep the iron still when you melt it. - Q. My solder melts into the space between my lead.
A. You have cut your lead too short or not at the right angle, and the gap is too big to fill with solder. You can patch this up with a small piece of scrap lead. Cut it a bit bigger than you need so that it balances over the gap. Now solder over it. This takes a bit of practice. (see photo above) - Q. My solder rolls off and won’t stick.
A. Either you don’t have enough flux, or the joint is still dirty. Try more flux, and if it still doesn’t stick, then clean it again with a wire brush. - Q. My iron isn’t melting the stained glass solder.
A. Your tip may be dirty or have excess solder on it. Clean it by wiping it on a damp cloth. Or the thermostat is set too low. Turn it up a little and wait before testing it on a scrap piece of lead.
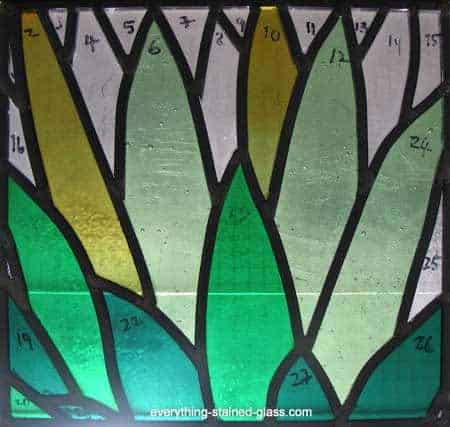
Helpful Resources
If you’re not sure which soldering iron is best for you, there’s a page here that will help answer your questions.
I’ve found a video that will give you an idea of how to solder stained glass, although I’m not too sure how good the joints are in the background – one looks a bit melted!
Video showing how to solder stained glass
Go to Cementing A Lead Came Panel if your piece is going to be exposed to the elements or installed in a building and needs to be weatherproof
Go to Cleaning and Polishing if you are going to hang it in a window and it’s small enough not to need strengthening with cement (no more than 12″ X 12″)
Hello Milly, thank you for all your tips but I cannot cut well. What saw would you recommend?
I recommend the Taurus Ring Saw, for the reasons on this page: https://everythingstainedglass.com/which-stained-glass-saw-do-you-recommend
But I WOULDN’T recommend getting a saw for regular cutting work, only for the 5 tasks on this page: https://everythingstainedglass.com/5-things-stained-glass-saws-well
I have lots of free cutting tutorials here: https://everythingstainedglass.com/how-to-cut-stained-glass
Or a short online cutting course here: https://www.everything-stained-glass-school.com/p/conquering-curves-1
Lots of suggestions LOL! I hope you find some help in there 🙂
Can you safely melt and remold lead crystal glass safely? Is it meltable and moldable? Thanks
You can melt and recast it Allison. It melts at a lower temp than say, float glass, so you’d have to search for an appropriate firing schedule.
Enjoying the videos which are helpful but could you tell me what oil I should use in my cutter please?
You can use 3 in 1 oil, lamp oil or buy dedicated cutting oil from stained glass suppliers Wendy. Some people don’t use oil at all!
I hope that helps.
Haven’t tried many types of fluids – obviously dedicated cutting oil is the best – one rhing to remember- if you ll be using the type of cutter filled with oil – make sure the end cap / lid is undone so the air gets in . Even better if you poor few drops into a small glass and keep the gutter head there . You won’t believe how many pieces of expensive glass i broke only because there was not enough oil . After i realized the mistake i made my glass cutting success improved by 60% .
A small piece of H lead came tilted during soldering allowing my small 1 inch bevel to slide out of place. It actually fell out of the panel when I picked it up! I did not notice that it tilted until I was soldering the back of the panel. How do I fix it? Thanks for any suggestions.
Ugh, the things that happen! If your panel is small enough to lift safely on one edge, use gravity to remove as much of the solder on the offending joint on the front and back. Then, with a very VERY sharp lead knife, cut along the joint front and back, thus freeing one edge of the lead. Wiggle bevel back in and re-solder, holding bevel steady!
I hope that helps.
Hi, I’ve had a go using a really small lead came. The piece looked great until I started to solder it. The lead melted and the piece was ruined. I managed to clean it off and ended up foiling the piece but is there a knack to soldering thus more fragile lead
Oh no, disaster! Yes, use a small soldering iron tip and turn it down so that you lessen the chance of melting the lead. I’m so sorry that happened Ann; narrow lead looks so gorgeous. Next time it will be different, don’t give up. Try practice piece of narrow lead first, playing with the heat.
I live on the Coast and have a continuing problem with oxidation on the lead caming when I start to solder a piece together. The solder literally explodes of the caming or forms balls that refuse to adhere. I’ve tried steel wool and sandpaper but neither have worked very welll. Do you have any suggestions for addressing this problem? Thanks
A wire brush is good for thoroughly cleaning the joints before soldering. Make sure you put the flux on straight away and solder soon after. It should fix it. Good luck Jeff.
Thanks Milly – I didn’t see your response until now. I’ve been cleaning with a wire brush and steel wool. This helps, but many times the solder sputters off even after the cleaning. I read that you can use mineral spirits to clean oxidation off copper foil. O one seems to know if it also works on lead caming, I think I’ll do a little experimenting. Do you have any experience with this.
Testing things first is good practice Jeff. I wouldn’t use mineral spirits (white spirit in UK) for tackling foil or lead oxidation. It makes a mess and doesn’t work.
Make sure your flux doesn’t have muriatic acid in it, it’s too caustic for lead. Most other fluxes contain an small amount of Hydrochloric acid which will also help clean oxidation from the lead.
Another thing you could try is to take a craft knife and scrape back the lead surface until it’s shiny. Be careful not to take too much off because it leaves less lead to solder and is easier to melt. Good luck and keep testing!
I’m working on a big piece can I solder part as I’m working or do I need to wait until the whole thing is constructed?
Lots of people I know work this way in copper foil, effectively using the multi-soldered piece as one piece of glass when they finally solder it together.
With lead came I always cut all, grind all (if necessary), lead all and solder all. As lead moves about a fair bit in construction I use that flexibility until the end, when I finally get everything to fit together. So I personally wouldn’t recommend soldering together areas before you put it all together with lead.
Good question Kristin, thanks.
Hi Jean,
Don’t panic! I’m assuming it’s a leaded piece as you say you’ve soldered just the joints? If so, you can’t remove it but you can touch them up and improve them.
Just make sure you have given the solder time to cool down before you go back to it.
Don’t move the soldering iron back and forth; it just makes a mess. Rather, keep it in the same place and hold it on the solder until it melts.
Then lift the iron tip vertically off the joint.
I hope that helps
Help!! I’ve got the same problem but I’ve only realised this after using blackening up with grate polish. Now its been blackened I can see that there’s too much solder on my piece of work. Have I ruined my piece or can it be saved by wire brushing the joints and melting the solder and running it off by holding it vertically. It’s supposed to be a surprise birthday present for my dad’s 80th in August…. I hope I can save it as I can’t remake it…
Please advise…
Lesley
You can clean the joints and redo at this late stage, yes. Use gravity as you say and (carefully) flick the solder off from the join. You run the risk of disturbing the cement underneath the lead in the process though.
Just one question: Have you put your piece up with the light behind it? Are you SURE there’s too much solder? Only I bet your dad wouldn’t even notice; he’ll just be amazed and overjoyed at your gift. Think about this before you do it Lesley!
I am desperate, the joints I soldered is all wrong, is there a way to remove all the solder and try again, otherwise the piece is no good.